In the world of metal casting, precision and functionality reign supreme, and one of the most significant innovations in this field is the process of "cast PF." This technique has transformed industries, offering a seamless and effective way to produce components with unmatched accuracy and durability. From its origins to its cutting-edge applications, cast PF stands as a testament to human ingenuity in engineering and manufacturing.
But what exactly is cast PF, and why is it so revolutionary? At its core, cast PF represents a specialized process that combines advanced casting methodologies with state-of-the-art materials to create components that are not only robust but also highly functional. This process has found applications in industries ranging from automotive to aerospace, and even in medical devices, where precision and strength are critical. Whether you're a manufacturer, an engineer, or simply someone curious about technology, understanding cast PF can open doors to a wealth of possibilities.
As we dive deeper into the topic, this article will unravel everything you need to know about cast PF—from its history and mechanics to its benefits and real-world applications. We'll also explore its environmental impact, emerging trends, and how it compares to other casting methods. By the end, you'll have a well-rounded understanding of this groundbreaking process and why it continues to shape the future of manufacturing.
Table of Contents
- The Origins and Evolution of Cast PF
- What is Cast PF? Understanding the Basics
- Advantages of Cast PF in Modern Industries
- Applications of Cast PF Across Different Sectors
- How Cast PF Compares to Traditional Casting Methods
- Materials Used in Cast PF: A Detailed Breakdown
- The Step-by-Step Process of Cast PF
- Essential Equipment and Tools for Cast PF
- Quality Control in Cast PF: Ensuring Perfection
- Environmental Impact of Cast PF
- Challenges and Limitations of Cast PF
- Emerging Trends and the Future of Cast PF
- FAQs About Cast PF
- Conclusion: The Lasting Impact of Cast PF
The Origins and Evolution of Cast PF
The story of cast PF is one of innovation, adaptation, and relentless pursuit of perfection. It all began with the need for more precise and durable casting methods, particularly in industries where traditional techniques fell short. Over the decades, researchers and engineers have refined the process, integrating new materials and technologies to enhance its efficiency and reliability.
Historical records indicate that the early iterations of cast PF were primarily used in the automotive sector to produce high-performance engine components. With time, its applications expanded to include aerospace, where the demand for lightweight yet strong materials drove further advancements. Today, cast PF is a versatile process employed in a wide range of industries, demonstrating its adaptability and importance in modern manufacturing.
Key Milestones in the Development of Cast PF
- Introduction of specialized alloys to improve casting quality.
- Integration of computer-aided design (CAD) for precise mold creation.
- Adoption of environmentally friendly materials and processes.
- Development of automated systems to enhance production efficiency.
The journey of cast PF is far from over, as ongoing research continues to push the boundaries of what's possible. With advancements in artificial intelligence and machine learning, the future of cast PF looks brighter than ever.
What is Cast PF? Understanding the Basics
At its core, cast PF is a highly specialized casting process designed to produce components with exceptional precision and durability. Unlike traditional casting methods, which often involve a degree of trial and error, cast PF leverages advanced technologies to ensure consistent quality and performance. But what sets it apart from other casting techniques?
One of the defining features of cast PF is its use of high-performance materials, which are carefully selected based on the specific requirements of the component being produced. These materials are melted, poured into precision-engineered molds, and then cooled under controlled conditions to achieve the desired shape and properties. The result is a component that meets or exceeds industry standards in terms of strength, functionality, and longevity.
Core Principles of Cast PF
- Precision: Achieving exact dimensions and tolerances.
- Durability: Producing components that can withstand extreme conditions.
- Efficiency: Minimizing waste and maximizing productivity.
Whether you're manufacturing complex aerospace parts or simple machine components, cast PF offers a reliable and efficient solution that meets the demands of modern industries.
Advantages of Cast PF in Modern Industries
Cast PF has revolutionized the way industries approach manufacturing, offering a multitude of advantages that make it a preferred choice for many applications. From cost savings to improved performance, the benefits of this process are both tangible and far-reaching.
Key Benefits of Cast PF
- Enhanced Precision: Achieve exact specifications with minimal errors.
- Cost-Effectiveness: Reduce material waste and production time.
- Versatility: Suitable for a wide range of materials and applications.
- Environmental Sustainability: Incorporates eco-friendly practices and materials.
In addition to these benefits, cast PF also offers the flexibility to produce both small and large-scale components, making it an ideal choice for industries with diverse manufacturing needs.
Applications of Cast PF Across Different Sectors
The versatility of cast PF has made it a cornerstone in various industries, each leveraging its unique advantages to meet specific challenges. From automotive to healthcare, the applications of cast PF are as diverse as they are impactful.
Industries That Rely on Cast PF
- Automotive: High-performance engine components.
- Aerospace: Lightweight and durable aircraft parts.
- Healthcare: Precision medical devices and implants.
- Energy: Components for renewable energy systems.
Each of these industries has its own set of requirements, and cast PF has proven its ability to meet and exceed expectations, cementing its place as a vital manufacturing process.
How Cast PF Compares to Traditional Casting Methods
When compared to traditional casting techniques, cast PF offers several distinct advantages that set it apart. While both methods aim to produce functional components, the differences in quality, efficiency, and environmental impact are striking.
Key Differences
- Quality: Cast PF delivers superior precision and durability.
- Efficiency: Faster production times and reduced waste.
- Sustainability: Incorporates eco-friendly materials and practices.
These differences make cast PF a compelling choice for industries looking to stay ahead of the curve in a competitive market.
Materials Used in Cast PF: A Detailed Breakdown
The choice of material is a critical factor in the success of any casting process, and cast PF is no exception. From metals to composites, the materials used in this process are selected based on their performance characteristics and suitability for the intended application.
Commonly Used Materials
- Aluminum: Lightweight and corrosion-resistant.
- Steel: Strong and durable.
- Titanium: High strength-to-weight ratio.
- Composites: Tailored for specific performance requirements.
Understanding the properties of these materials is essential for optimizing the cast PF process and achieving the desired results.
The Step-by-Step Process of Cast PF
The cast PF process involves several meticulously planned steps, each contributing to the overall quality and functionality of the final product. From material selection to finishing, every stage is designed to ensure precision and efficiency.
Stages of the Cast PF Process
- Material Selection: Choosing the right material for the job.
- Mold Design: Creating a precise mold using CAD software.
- Casting: Melting and pouring the material into the mold.
- Cooling: Allowing the material to solidify under controlled conditions.
- Finishing: Removing excess material and polishing the component.
Each of these steps is critical to the success of the cast PF process, ensuring that the final product meets all specifications and requirements.
Essential Equipment and Tools for Cast PF
The success of the cast PF process depends not only on the materials and techniques used but also on the equipment and tools involved. From furnaces to molds, each piece of equipment plays a vital role in ensuring the quality and efficiency of the process.
Key Equipment
- Furnaces: For melting the materials.
- Molds: Precision-engineered for accurate casting.
- Cooling Systems: To control the solidification process.
- Finishing Tools: For polishing and refining the final product.
Investing in high-quality equipment is essential for optimizing the cast PF process and achieving consistent results.
Quality Control in Cast PF: Ensuring Perfection
Quality control is a cornerstone of the cast PF process, ensuring that each component meets stringent standards for performance and durability. From material testing to final inspection, every stage of the process is subject to rigorous quality checks.
Quality Control Measures
- Material Testing: Ensuring the suitability of the selected materials.
- Dimensional Analysis: Verifying the accuracy of the component's dimensions.
- Performance Testing: Assessing the component's functionality under real-world conditions.
These measures help maintain the integrity of the cast PF process, ensuring that each component meets or exceeds industry standards.
Environmental Impact of Cast PF
As industries around the world shift towards more sustainable practices, the environmental impact of manufacturing processes has come under scrutiny. Cast PF is no exception, and efforts are being made to minimize its ecological footprint.
Eco-Friendly Practices
- Using recyclable materials.
- Reducing waste through precise casting techniques.
- Incorporating energy-efficient equipment.
By adopting these practices, the cast PF process is becoming more sustainable, aligning with global efforts to protect the environment.
Challenges and Limitations of Cast PF
While cast PF offers numerous advantages, it is not without its challenges and limitations. Understanding these issues is crucial for optimizing the process and overcoming potential obstacles.
Common Challenges
- High Initial Costs: Investment in equipment and materials can be expensive.
- Complexity: Requires specialized knowledge and skills.
- Material Limitations: Not all materials are suitable for cast PF.
Addressing these challenges is essential for maximizing the benefits of the cast PF process and ensuring its long-term viability.
Emerging Trends and the Future of Cast PF
The future of cast PF is bright, with numerous advancements on the horizon. From the integration of artificial intelligence to the development of new materials, the possibilities are endless.
Future Trends
- AI-Driven Optimization: Enhancing the efficiency and precision of the process.
- New Materials: Developing alloys and composites with superior properties.
- Automation: Streamlining the production process through advanced robotics.
These trends promise to revolutionize the cast PF process, making it more efficient, sustainable, and versatile than ever before.
FAQs About Cast PF
1. What is the primary advantage of cast PF?
The primary advantage of cast PF is its ability to produce highly precise and durable components, making it ideal for industries with stringent quality requirements.
2. Which industries benefit the most from cast PF?
Industries such as automotive, aerospace, healthcare, and energy benefit significantly from cast PF due to its versatility and precision.
3. How does cast PF contribute to environmental sustainability?
Cast PF incorporates eco-friendly practices such as using recyclable materials, reducing waste, and employing energy-efficient equipment.
4. What are the main challenges associated with cast PF?
The main challenges include high initial costs, complexity, and material limitations.
5. What materials are commonly used in cast PF?
Commonly used materials include aluminum, steel, titanium, and specialized composites.
6. What advancements are shaping the future of cast PF?
Advancements such as AI-driven optimization, new materials, and automation are shaping the future of cast PF, making it more efficient and versatile.
Conclusion: The Lasting Impact of Cast PF
Cast PF is more than just a manufacturing process; it's a testament to human ingenuity and the relentless pursuit of perfection. With its numerous advantages, wide-ranging applications, and potential for future advancements, cast PF continues to shape the landscape of modern industries. As we look to the future, the possibilities for this groundbreaking process are endless, promising a world of innovation and excellence.
You Might Also Like
Riding The Humor Wave: The Phenomenon Of Ebike MemesScream Memes: The Viral Phenomenon With Endless Laughter
The Ultimate Guide To Refresco Caballito: A Refreshing Mexican Tradition
Eco-Friendly And Versatile Popcorn Bags For Every Occasion
Jason Tatom: A Rising Star In The World Of Basketball
Article Recommendations
- How The Concept Of Resonate Meaning Impacts Communication And Connection
- Mobile Mike The Gamechanger In Digital Marketing For 2024
- Avatar Dragon The Mythical Icon Of Power And Majesty
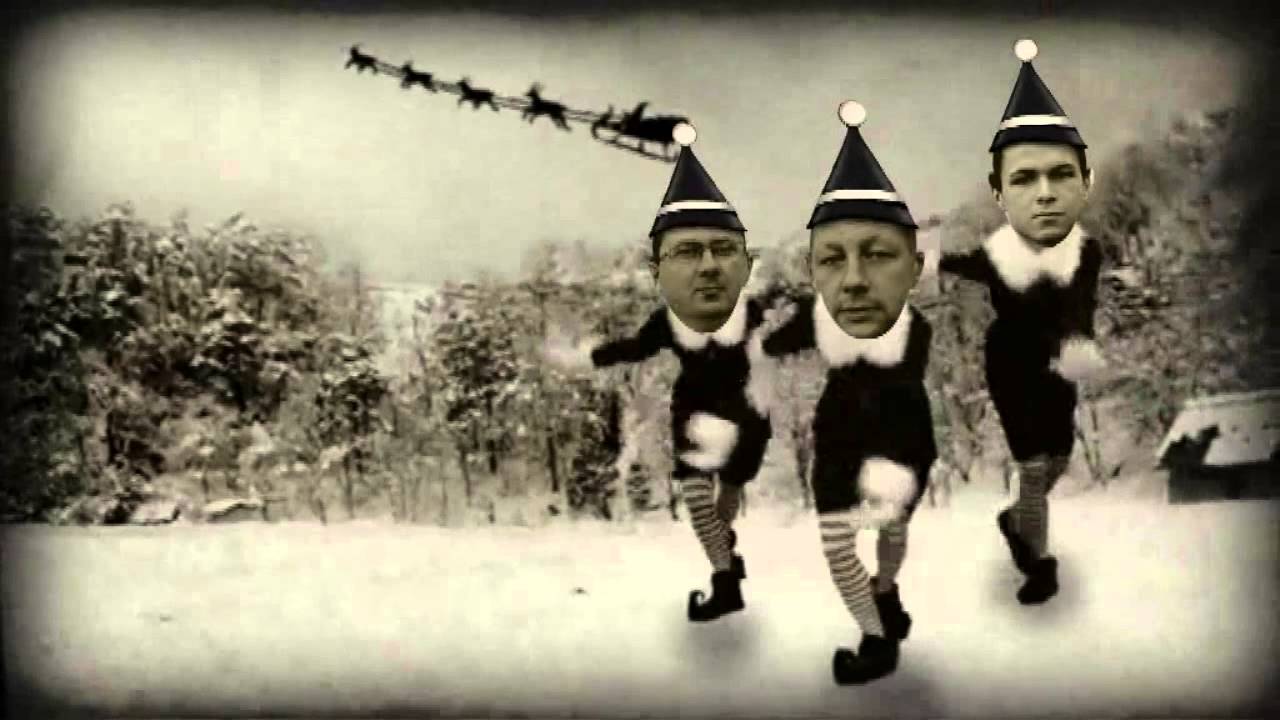
